Lean manufacturing is a production management method that focuses on maximizing value for the customer while eliminating waste. Based on the principles and tools of the Toyota Production System (TPS), lean aims to create a smooth flow of materials and efficient processes to meet customer demands. In this article, we will explore what lean manufacturing is, its connection to TPS, the industries using it, and the benefits companies see from implementing lean principles.
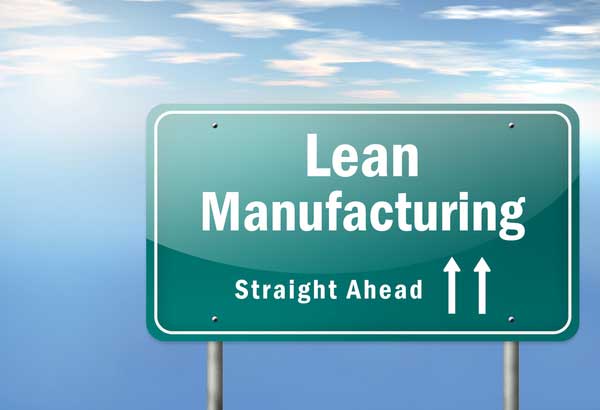
What is Lean Manufacturing?
Lean manufacturing is a production management philosophy that originated in Japan, predominantly in the Toyota automotive company. It is focused on reducing 7 major types of waste: overproduction, waiting time, transportation, over-processing, inventory, motion and defects. The core idea is to maximize customer value while minimizing waste.
Lean sees any activity that does not add value to the final product as waste. This waste is stripped out of production and business processes. The desired result is to improve quality, eliminate waste, reduce production time and cost, and respond faster to consumer demands.
The term “lean production” was first coined in 1988 by John Krafcik to describe Toyota’s production system compared to craft or mass production systems. In 1990, in their book “The Machine That Changed the World,” James Womack and Daniel Jones popularized the concepts of lean production and thinking. Their research showed the superior performance of Japanese automakers in productivity, quality and flexibility compared to Western mass production systems. This demonstrated the power of the lean production model.
Principles of Lean Manufacturing
The core principles of lean manufacturing are:
- Define value from the customer’s perspective
- Map the value stream and identify waste
- Create flow in production processes
- Use a pull system to avoid overproduction -Seek perfection through continuous improvement
These principles guide organizations on their journey towards lean operations. The main goal is to provide the customer with exactly what they want, when they want it, and avoid any waste in the process.
Tools for Lean Manufacturing
There are a variety of lean tools and techniques that help put the core principles into practice:
- 5S – Workplace organization method
- Value stream mapping – Map process flow and find waste
- Total productive maintenance – Keep equipment operating smoothly
- Single minute exchange of die – Reduce changeover times
- Poka-yoke – Mistake proofing
- Kanban – Pull system for materials and production
- Kaizen – Continuous improvement
These tools work together as a system to create lean processes. 5S creates an orderly workplace for efficiency. Value stream mapping analyzes the flow to show opportunities to eliminate waste. Total productive maintenance keeps machines running smoothly. Single minute exchange of die reduces changeover times between products. Poka-yoke prevents defects by mistake proofing processes. Kanban links processes in a pull system. Kaizen encourages continuous improvement at all levels.
Connection to the Toyota Production System
The Toyota Production System laid the foundations for lean manufacturing. Toyota developed its production system in the aftermath of World War II when resources were scarce. They focused on eliminating waste to get the most out of what they had available.
The two pillars of TPS are Jidoka and Just-in-Time (JIT). Jidoka means automation with a human touch. Processes are designed to stop immediately if abnormalities occur to prevent defects. JIT means only producing what is needed when it is needed. This avoids overproduction and excess inventory.
TPS uses techniques like Kanban cards to link production processes in a pull system. Production is smoothed with Heijunka which levels the type and quantity of production. Toyota focused on small batches and rapid changeovers to respond flexibly to demand. Continuous improvement underpins it all.
Many of the tools and principles used in lean manufacturing come directly from innovations developed by Toyota. Lean has taken these concepts that revolutionized automobile manufacturing and extended them to many other industries.
Industries Using Lean Manufacturing
Though lean originated in automotive, its techniques have spread far beyond. Lean principles and tools have been applied successfully in manufacturing, services, healthcare, government, military, construction and more. Some examples include:
Manufacturing – electronics, appliances, aerospace, machinery, furniture, metal fabrication Services – banking, insurance, hospitality, restaurants Healthcare – hospitals, medical offices, clinics Military and Government – military logistics and operations, public services Construction – residential, commercial, infrastructure
The benefits of eliminating waste while focusing on the customer transcend specific industries. Almost any organization can find ways to implement lean thinking to improve their processes. Even such complex systems as healthcare and defense are using lean principles as a major driver of improvement.
Benefits of Lean Manufacturing
Research by the Lean Enterprise Institute Poland based on over 50 case studies found impressive results from implementing lean manufacturing including:
- Increased productivity by up to 66%
- Improved machine usage up to 59%
- Reduced inventory levels by up to 80%
- Decreased production space needs by up to 61%
- Faster raw material to finished product by up to 70%
- Reduced changeover times up to 96%
Additional benefits reported were better quality, fewer defects, more employee ideas for improvement, enhanced communication and large reductions in waste.
The benefits of lean manufacturing derive from eliminating the 7 major wastes. Less human labor is needed, production and inventory space is reduced, and engineering time is minimized. Products flow smoothly through processes designed based on customer demand rather than internal constraints.
Continuous improvement empowers workers at all levels to identify and eliminate waste. This culture of improvement optimizes processes and allows companies to achieve short production times, top quality, and low costs compared to traditional approaches.
The Pursuit of Perfection with Lean
Lean manufacturing offers a proven system to strive for perfection in meeting customer value. The practices originated by Toyota have transformed automotive manufacturing and been widely adopted across industries. Though the journey requires commitment, the lean approach delivers major improvements in productivity, quality and flexibility.
By focusing on waste reduction and empowering employees, lean provides a clear path to creating smooth, streamlined processes. Standardization, visual controls and mistake proofing create robust processes. Rapid changeovers and small batches allow adjusting swiftly to changes in customer demand.
For any organization, lean manufacturing gives a way to continuously improve processes in the pursuit of perfection. With diligent practice of lean principles and tools, the sky is the limit for enhancing value and delighting customers. Lean sets in motion a cycle of improvement that can adapt to changing needs and prioritize value without sacrificing efficiency, quality or speed.