In today’s fast-paced world, industrial companies are constantly seeking ways to improve their competitiveness, efficiency and adaptability. The 6S Lean Management System, a management method widely used by Toyota and many other Japanese companies, helps achieve this goal. 6S is composed of Sort, Set in Order, Shine, Standardize, Sustain and Safety.
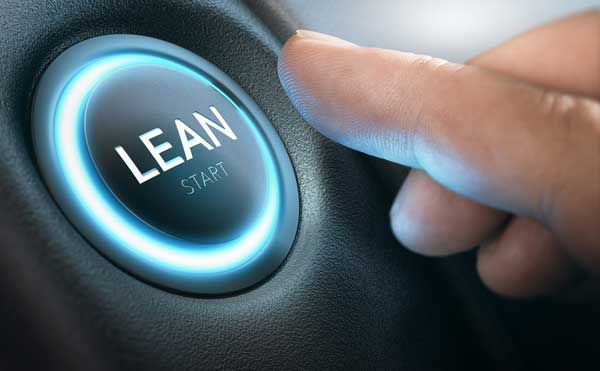
What is 6S Lean Management System
The 6S Lean Management System is a workplace organization methodology that helps optimize workflow and reduce waste. The six aspects of 6S help organize tools and materials, clean the work environment, standardize best practices, sustain the 6S system, and promote workplace safety.
Implementing 6S leads to increased productivity, quality, and safety along with reduced costs and waste. It also contributes to higher employee engagement and satisfaction by improving the work environment.
Overview of Our Prototype & Low-Volume Production Workshop
Unlike large manufacturers that produce the same products for long periods, our workshop specializes in prototype development and low-volume production. We constantly dispose of damaged tools and equipment that cannot be repaired while also classifying nonconforming and conforming products.
As a prototype manufacturer, we produce hundreds of different parts every month across a large number of projects daily. We utilize extensive CNC machinery, sanding and polishing areas with abundant sandpaper and tools. Careful organization of our workplace is critical for efficiency.
Implementing the Six 6S Pillars in Our Workshop
Sort
We begin implementing 6S by sorting through all tools, materials, and equipment. We mark and separate raw materials, semi-finished products from each production step, and finished products. This progress tracking confirms our manufacturing status.
Cutting tools and instruments are neatly arranged while raw materials are organized by their corresponding projects to prevent confusion. Damaged, obsolete, or unnecessary items are disposed of or removed from the main workspace.
Set in Order
With sorting completed, we assign everything a proper place in our workshop. We consider item usage frequency and production workflow when determining location. Related components are grouped together, with visual controls established for quick identification. Shadow boards, floor markings, and customized storage solutions all help set order.
Shine
Our daily schedule includes time dedicated to cleaning work areas and machinery. Pathways, desks, equipment, and tools are all cleaned to maintain a dirt-free workspace. Preventative maintenance on machines ensures optimal performance while inspection and organization of tools guarantees their availability.
Standardize
We combine the first three S pillars of sort, set in order, and shine to establish standardized workflows. Documenting best practices around tool usage, cleaning procedures, storage locations, and general operations leads to steady improvements over time.
As a medium-sized factory, we also implement a system of rewards and consequences for following 6S protocols while regularly evaluating execution. This promotion of continuous improvement is critical for success.
Sustain
Transitioning 6S from a one-time program to an intrinsic way of working sustains the benefits. We mandate grooming standards while also conducting spirit building activities to motivate employees. Developing strong habits, team cohesion, and engagement around 6S principles is key.
Safety
Emphasizing safety is pivotal when operating machinery and tools for manufacturing. We prominently display caution signs, have comprehensive emergency response plans, and regularly conduct safety training sessions.
Promoting a culture of safety where everyone looks out for themselves and others eliminates accidents and injuries while boosting morale.
The Benefits of 6S System Implementation
Carefully and conscientiously following the 6S framework leads to major efficiency and safety improvements in our manufacturing workshop. Specifically, we realized benefits like:
- Streamlined production lines and machinery
- Organized tools and materials
- Clear responsibility assignment
- Reduced waste
- Improved quality
- Enhanced productivity
- Increased employee satisfaction
The structure and discipline of 6S change the workplace culture to one of continuous improvement. Our workshop is demonstrably more organized, clean, efficient, and safe after implementing the four S pillars.
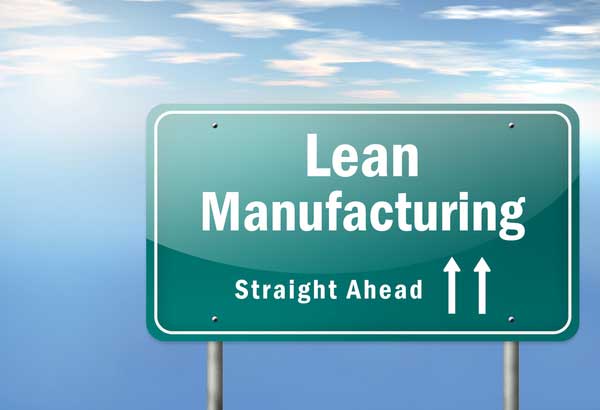
Try 6S in Your Manufacturing Environment
The 6S Lean Management System has produced major tangible and intangible benefits for our low-volume production workshop, and it can do the same for all types of manufacturing. Consider adopting a 6S workplace organization program to optimize efficiency, reduce waste, and improve safety. The productivity and quality gains are certainly worthwhile.